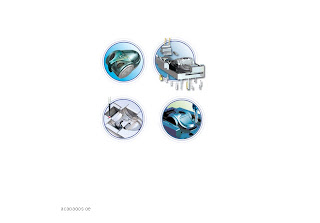
Delcam Plc es el proveedor de soluciones CADCAM para el diseño, manufactura, inspección e ingeniería inversa de formas complejas y moldes líder en el mundo.
Un reporte reciente del analista líder en EE.UU., CIMdata, público que Delcam es el proveedor CADCAM numero 1 de América del Norte y Europa, y numero 3 en Asia. Delcam tiene más de 125 oficinas de soporte locales en más de 80 países alrededor del mundo.
Delcam es uno de los proveedores líderes de soluciones para el desarrollo de producto en la industria manufacturera. La compañía ha crecido constantemente desde que fue formalmente fundada en 1977, luego de un desarrollo inicial para la Universidad de Cambridge. Hoy es el mayor desarrollador de software de diseño y producción en el Reino Unido, con subsidiarias en América del Norte, Europa y Asia.
Delcam es utilizado por más de 9.000 organizaciones en más de 80 países. Estos clientes varían desde corporaciones multinacionales hasta diseñadores y matriceros particulares, y son de un amplio rango de industrias, incluyendo aeronáutica, automotriz, aplicaciones eléctricas, calzado, cerámicos, envases, juguetes, equipos deportivos, joyería y señalización. Delcam ha sido largamente reconocido común especialista en la producción de soluciones de diseño para compañías que utilizan formas complejas y ergonómicas, así como también por ser el proveedor numero uno del mundo de sistemas CADCAM para la matriceria y fabricación de moldes.Vea como Delcam ayudo a otras compañías en su industria.
La llave del éxito de la compañía ha sido desde siempre la predisposición para solucionar las necesidades del cliente. Además de proveer el más alto nivel de entrenamiento y soporte a través de su red de más de 125 revendedores alrededor del mundo, Delcam dedica el 50% de las ganancias de su software en mejoras en el desarrollo de su software. Este nivel de inversión asegura que el software de Delcam se mantenga en su posición de líder mundial.
Todos los empleados de Delcam traban junto con sus clientes para entender las necesidades con más precisión, y para poder responder más rápida y efectivamente a los cambios en sus métodos de diseño y manufactura. Además, Delcam es el único proveedor CADCAM internacional que opera con su propio taller de ingeniería, La División de Servicio de Mecanizado de Delcam permitiendo probar todo el software antes de sus lanzamientos. Este centro, elaborado con relaciones cercanas con proveedores de maquinas herramientas y otros equipos relacionados, le da a los empleados de Delcam un conocimiento único de los problemas que deben enfrentar los usuarios y asi permite un mejor desarrollo de las soluciones.
Un reporte reciente del analista líder en EE.UU., CIMdata, público que Delcam es el proveedor CADCAM numero 1 de América del Norte y Europa, y numero 3 en Asia. Delcam tiene más de 125 oficinas de soporte locales en más de 80 países alrededor del mundo.
Delcam es uno de los proveedores líderes de soluciones para el desarrollo de producto en la industria manufacturera. La compañía ha crecido constantemente desde que fue formalmente fundada en 1977, luego de un desarrollo inicial para la Universidad de Cambridge. Hoy es el mayor desarrollador de software de diseño y producción en el Reino Unido, con subsidiarias en América del Norte, Europa y Asia.
Delcam es utilizado por más de 9.000 organizaciones en más de 80 países. Estos clientes varían desde corporaciones multinacionales hasta diseñadores y matriceros particulares, y son de un amplio rango de industrias, incluyendo aeronáutica, automotriz, aplicaciones eléctricas, calzado, cerámicos, envases, juguetes, equipos deportivos, joyería y señalización. Delcam ha sido largamente reconocido común especialista en la producción de soluciones de diseño para compañías que utilizan formas complejas y ergonómicas, así como también por ser el proveedor numero uno del mundo de sistemas CADCAM para la matriceria y fabricación de moldes.Vea como Delcam ayudo a otras compañías en su industria.
La llave del éxito de la compañía ha sido desde siempre la predisposición para solucionar las necesidades del cliente. Además de proveer el más alto nivel de entrenamiento y soporte a través de su red de más de 125 revendedores alrededor del mundo, Delcam dedica el 50% de las ganancias de su software en mejoras en el desarrollo de su software. Este nivel de inversión asegura que el software de Delcam se mantenga en su posición de líder mundial.
Todos los empleados de Delcam traban junto con sus clientes para entender las necesidades con más precisión, y para poder responder más rápida y efectivamente a los cambios en sus métodos de diseño y manufactura. Además, Delcam es el único proveedor CADCAM internacional que opera con su propio taller de ingeniería, La División de Servicio de Mecanizado de Delcam permitiendo probar todo el software antes de sus lanzamientos. Este centro, elaborado con relaciones cercanas con proveedores de maquinas herramientas y otros equipos relacionados, le da a los empleados de Delcam un conocimiento único de los problemas que deben enfrentar los usuarios y asi permite un mejor desarrollo de las soluciones.